技術コラム
金属部品の樹脂化による軽量化: メリットと開発のポイント
2025.04.02
製品設計において、金属から樹脂への置き換え(樹脂化)は注目される軽量化手法です。最近のエンジニアリングプラスチックの発展により、従来は金属が使われていた部品もプラスチック製に置き換えて必要な性能を維持しつつ軽量化・コストダウンを実現できるようになってきました。
弊社でも金属からの代替として樹脂化のご相談を多く頂いております。強度を確保した軽量化について試作段階からご支援可能です。
金属から樹脂への置き換えとは?
「金属部品の樹脂化」とは、その名の通り金属製だった部品をプラスチック製に変更することです。鉄やアルミなど高い強度・耐熱性が必要な部分に使われてきた金属を、高機能な樹脂素材に代替することで、性能を保ちながら部品の軽量化、部品点数の削減、塗装・メッキレス化、コスト低減などの効果が得られます。
素材そのものの比重を比較すると、樹脂は金属より格段に軽量です。例えば鉄(比重7.8)から樹脂(1.3〜1.4程度)に置き換えると重量は約1/5〜1/6になり、アルミ(比重2.7)からでも約1/2に軽くできます。このような大幅な軽量化が可能なため、自動車業界をはじめ様々な産業で金属部品の樹脂化が進められています。また、樹脂化によって製品設計の自由度も向上し、複雑形状の一体成形や部品統合による工程簡略化にもつながります。
軽量化のメリット
金属から樹脂への材料置換により得られる軽量化のメリットは多岐にわたります。
- 省エネルギー・燃費向上: 製品が軽くなることで移動や駆動に必要なエネルギーが減少し、燃費や電費の改善に直結します。自動車では車両重量を削減することで少ない燃料で長く走行でき、CO₂排出削減にも貢献します。製品重量の低減は輸送時のコスト削減や環境負荷の低減にもつながります。
- 扱いやすさ・作業性向上: 軽い部品は人が扱いやすく、生産現場での組み立て作業の負担軽減や運搬性の向上につながります。実際、金属部品を樹脂(PPS)に変更して重量を半減させた結果、従来は重量物だった部品を女性作業者でも容易に扱えるようになった例もあります。ユーザーが製品を持ち運ぶ場合も、軽量化は大きな利点です。
- コスト削減: 樹脂は一般に材料単価が金属より安価な場合が多く、加工工程も射出成形など一工程で完結するため、量産時の製造コストを抑えられる可能性があります。金属加工では切削・溶接・研磨・メッキなど複数の工程が必要ですが、樹脂成形なら金型による一発成形が可能で、組立工数の削減や副資材の削減にも寄与します。大量生産では一度に多くの部品を同時成形できるため、生産効率も向上します。
- 設計自由度の向上: 樹脂成形では金型設計次第で金属では難しい複雑な形状や一体構造を実現できます。その結果、従来は分割して組み立てていた形状を一体化して成形することが可能となり、部品点数削減による信頼性向上やコストダウンが見込めます。また樹脂は錆びない・着色しやすい・電気絶縁性が高いといった特性もあり、これらも付随的なメリットと言えるでしょう。
このように、樹脂化による軽量化は省エネ性能や使い勝手、コスト面で大きなメリットをもたらし、さらに設計上の新たな自由度を生み出します。
3. 耐久性の懸念点と解決策
一方で、「プラスチックに置き換えて強度や耐久性は大丈夫か?」という懸念も生じます。樹脂は金属に比べて柔らかく熱に弱いイメージがありますが、近年のエンジニアリングプラスチックは大幅に性能が向上しています。ガラス繊維や炭素繊維で強化された樹脂は比強度(強度/重量)でアルミダイキャストに匹敵するものも開発されており、適切に設計すれば金属代替に十分な強度・剛性を持たせることができます。
耐久性を確保するポイントとして、まず材料選定が重要です。使用環境に合わせて耐熱温度や機械的強度、耐摩耗・耐候性に優れた樹脂を選びましょう。例えば高温環境の部品には耐熱性の高い樹脂を、荷重がかかる構造部品にはガラス繊維強化グレードなど高強度な樹脂を選定します。必要に応じて金属並みの強度が出せるスーパーエンプラを採用することで、「金属だからこそ実現できていた性能」を樹脂でも満たせるようにします。
次に強度設計の工夫です。単に金属部品と同じ形状・肉厚で樹脂に置き換えるだけでは十分な強度が出ない場合が多いため、樹脂特有の特性を踏まえた設計変更が必要になります。具体的には、肉厚を適切に増やしたりリブ(肋骨状の補強肋)を配置して剛性を高める、コーナー部に丸みをつけて応力集中を緩和する、といった形状上の工夫が挙げられます。樹脂は成形収縮や温度変化による歪みが発生しやすいため、寸法精度が要求される箇所には補強リブやボスを設けて変形を抑制したり、公差に余裕を持たせる設計が有効です。また、ネジ部や軸受け部分など高荷重のポイントには金属インサートを埋め込んで耐久性を補強することも一般的です。
さらに、近年はCAE解析(構造解析や流動解析)の活用により、試作前に樹脂部品の強度や変形をシミュレーションして問題点を洗い出すことも可能になっています。こうした設計技術や補強方法を駆使すれば、樹脂化による軽量化と必要な強度・耐久性の両立が十分に可能です。弊社でもCAE解析によるシミュレーションを取り入れております。
4. アルミ代替として使用される主な樹脂材料
アルミニウムなど金属材料の代替に適した高性能樹脂として、以下のようなエンジニアリングプラスチックが代表的です。
- PPS
耐熱温度が220〜240℃と高く、優れた剛性・強度を持つスーパーエンプラです。金属並みの強度でありながら軽いという特性があり、さらに金属より安価な場合もあるため、軽量化とコストダウンを目的に金属部品の代替材料として広く用いられています。耐薬品性・耐疲労性(繰り返し荷重に対する強さ)・耐クリープ性にも優れるため、ポンプやバルブ部品、モーター筐体など金属さながらの耐久性が求められる用途に適しています。ただし成形性がやや難しく、金型設計にはノウハウが必要です。 - PEEK
樹脂の中でもトップクラスの性能を持つスーパーエンプラです。連続使用温度が約250℃にも達し、耐薬品性や難燃性にも非常に優れます。機械的強度も極めて高く、引張強度約90MPaはアルミ合金(A6063-O)と同等との報告があります
。このように金属に匹敵する特性を持つため、航空宇宙や自動車、産業機器の部品で金属の代替として使用されます。耐摩耗性や疲労寿命も長く、金属では必要だった潤滑やメンテナンスを省ける場合もあります。ただし材料コストが高価で、加工にも高温対応の設備が必要となるため、用途は限定されます。 - PA6 + GF(ガラス繊維強化ナイロン6)
ポリアミド(ナイロン)は汎用エンジニアリングプラスチックの中で特に強度・靭性に優れ、ガラス繊維で強化することでさらに剛性や耐熱性を高めた材料です。強化ナイロンは自動車の金属部品代替材料として近年特に注目されており
、実際にエンジンのインテークマニホールドやエンジンカバーなどでアルミから樹脂への置き換えが進んでいます。耐熱性はガラス繊維30%強化品で120〜150℃程度まで対応し、衝撃強度や耐摩耗性にも優れるバランスの良い素材です。高強度ナイロン樹脂を採用してアルミ製部品から置き換えた事例では、約60%もの軽量化を達成したケースもあります
。
上記の他にも、PC(ポリカーボネート)やPOM(ポリアセタール)、PA66(ナイロン66)、PEI(ポリエーテルイミド)など、用途に応じて様々な樹脂が金属代替に利用されています。それぞれの材料特性(耐熱性、強度、靭性、耐薬品性など)を把握し、置き換え対象の金属部品が要求する性能を満たせる樹脂を選定することが重要です。
5. 樹脂化に適した製品事例(自動車部品・家電・産業機器など)
実際に金属から樹脂への置き換えが進んでいる製品分野の事例をいくつか紹介します。
自動車エンジンの樹脂製インテークマニホールドの例(黒い吸気マニホールド部分が樹脂成形で作られており、中央の銀色のスロットルボディは金属製)。このような耐熱・高強度樹脂部品がエンジン周辺に多数採用されています。
- 自動車部品: 軽量化ニーズが特に高い自動車分野では、多くの金属部品が樹脂へ置き換えられてきました。例えばエンジンのインテークマニホールド(吸気管)は1990年代後半からアルミ製から樹脂製への移行が進み、現在では国内生産車の約9割が樹脂製を採用しています。樹脂製インマニはアルミ製に比べ約60%の軽量化を達成しつつ、エンジンルームの限られたスペースに合わせて複雑な形状を一体成形できるため、性能向上とレイアウト自由度の両立に貢献しています。この他にも、エンジンカバーやラジエータータンク、オイルパン、ブラケット類、さらに電気自動車のバッテリーケースに至るまで、樹脂化の事例が広がっています。車両全体の軽量化による燃費向上だけでなく、低重心化による走行安定性向上など副次的なメリットも得られています。
- 家電製品: 家庭用電化製品でも、金属シャーシや機構部品を樹脂化することで軽量化とコスト削減が進んでいます。例えば洗濯機のフレームやドラム支持部品、掃除機・芝刈り機などの筐体(外装)、エアコンや給湯器の機構部品などが樹脂化の例です。樹脂は絶縁性が高く錆びないため、電子レンジや炊飯器の内部構造体、配線を保持する部品などにも適しています。実例として、給湯器のバルブ部品やポンプモーターのカバー、エアコンの温度調節部品など、従来金属が使われていた高温部品をPPS樹脂に置き換えて製造しているケースがあります。これらはいずれも耐熱性能と成形精度が求められる部品ですが、適切な材料選定と金型設計により金属同等の性能を発揮しています。
- 産業機器: 工場の生産設備や各種機械装置でも、軽量化・省エネやメンテナンス性向上を目的に樹脂化が進んでいます。例えばロボットのアーム部品や自動搬送装置のフレーム、製造装置内で使われるギア・カム機構などが樹脂製に置き換えられています。金属製のナット・ボルトを樹脂製に変更して絶縁性や防錆性を高めたり、液体を扱うポンプのインペラー(羽根車)を樹脂製にして慣性質量を減らすといった例もあります。産業機器では、一部を樹脂化することで装置全体の重量を抑えて設置や輸送を容易にしたり、可動部の負荷を減らしてモーターの小型化・省電力化を図る効果が期待できます。
以上のように、多様な分野で樹脂化の成功事例が存在します。樹脂への置き換えによって重量低減だけでなく新たな付加価値(設計の柔軟性向上、加工工程の簡素化、防錆・絶縁性の付与など)が生み出されている点に注目できます。
樹脂化を成功させるポイント(材料選定・試作・量産移行)
金属部品の樹脂化プロジェクトを成功させるためには、いくつかの重要なポイントがあります。特に「材料選定」「試作評価」「量産移行」の3点が鍵となります。
① 材料選定
最初のステップは、置き換え対象となる金属部品の要求性能を満たす適切な樹脂材料を選ぶことです。使用環境(温度域、負荷条件、屋内外、接触する薬品など)を詳細に洗い出し、それらに耐えうる樹脂を絞り込みます。
例えば高温環境であれば耐熱グレードのPPSやPEEK、衝撃荷重が大きければ靭性に優れたPCやPA、寸法精度重視なら吸湿が少なく剛性の高いPOM、といった具合に材料特性と用途要件のマッチングを行います。樹脂メーカー各社が豊富なグレードを展開しているため、必要に応じてデータシートや技術サポートを活用し、最適な素材を選定しましょう。
② 試作とテスト:
設計した樹脂部品は、試作による検証を必ず行います。既存の金属部品から樹脂化する場合、試作による評価は必須プロセスといえます。まず試作品を製作し、寸法精度や組み付け性、実使用環境での強度・耐熱性をテストします。試作方法としては、3Dプリンター造形や切削加工による樹脂試作、あるいはシリコン型を使った真空注型など、目的や数量に応じて様々な手法が活用できます。
特に強度評価には実材料での射出成形品が望ましいですが、コストや期間の制約がある場合は代替プロセスでも早期に試作して課題を発見することが大切です。試作評価により、設計段階では見えなかった問題点(変形や強度不足など)が判明することも多々あります。得られたフィードバックを設計に反映し、必要なら形状修正や材料グレード変更を行いましょう。十分な検証を経て金属品と同等の性能が確認できれば、本格的な量産へと進めます。
③ 量産への移行
試作・評価をクリアしたら、いよいよ量産プロセスへの移行です。量産用の金型を設計・製作する際には、樹脂特有の成形収縮や樹脂流動を考慮して微調整を行います(CAEによる流動解析を事前に実施しておくと安心です)。量産初期にはトライアル成形を重ね、量産条件下で品質に問題がないか最終確認します。
樹脂化した部品の量産では、金属加工には無かった品質管理項目(樹脂材料のロット管理、射出成形条件の管理など)が増えますので、製造部門と連携して管理体制を整えることも成功のポイントです。こうした段階を踏むことで、試作段階から量産体制へのスムーズな移行が可能になります。
以上のステップを着実に踏むことで、金属部品の樹脂化プロジェクトは成功へと近づきます。材料選びから試作・評価、量産化まで一貫して計画し、必要に応じて樹脂化の経験豊富なパートナーに相談することで、リスクを低減しつつ開発を進めることができるでしょう。
ギケンの強み(短納期対応・高精度試作・材料選定サポート)
弊社では、金属部品の樹脂化に取り組まれるお客様をトータルサポートいたします。長年にわたり多種多様な樹脂材料による製品開発支援を行っており、試作から量産まで一貫したサービスをご提供可能です。特に以下のような強みで、お客様の樹脂化プロジェクト成功を後押しします。
- 短納期対応
- 開発スピードの要求に応えるため、試作から量産まで迅速に対応します。社内に充実した設備とノウハウを備え、試作品の短期提供や金型製作期間の短縮に努めています。これにより、お客様のタイムラインに沿ったスピーディーな開発が可能です。
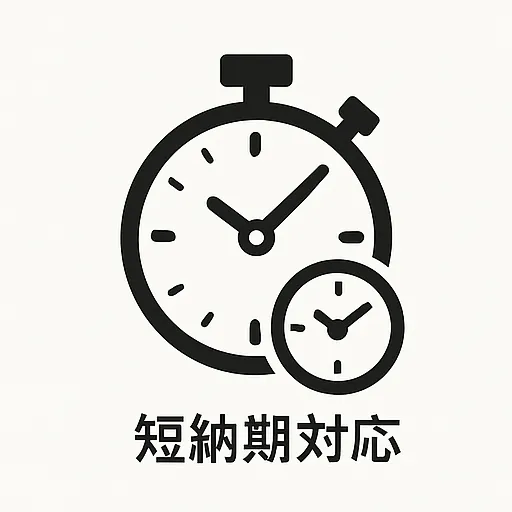
- 高精度な試作
- 弊社は精密な樹脂部品の試作技術を有しており、寸法精度・品質の高い試作品を製作します。金属部品との置き換えにおいて重要な嵌合精度や強度特性を正確に再現した試作品をご提供できるため、実機テストで有用なデータを得られます。試作段階での問題点抽出と改善提案により、量産移行時の手戻りを最小限に抑えます。
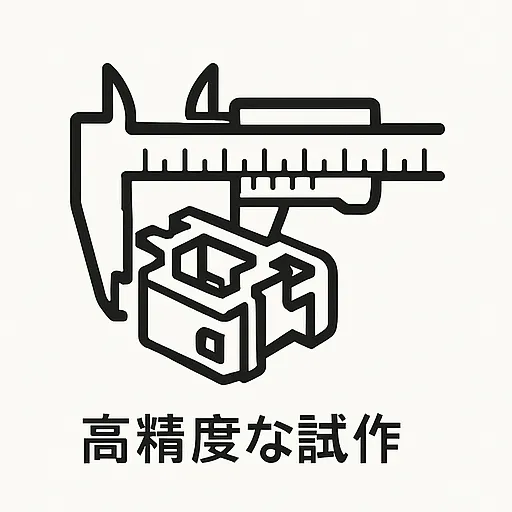
- 材料選定のサポート
- 豊富な材料知識を持つエンジニアが在籍し、要求される性能や用途に合わせて最適な樹脂材料の選定をサポートいたします。「どの樹脂を選べばいいか分からない」「金属の代替候補材料を比較検討したい」といった場合でも、材料特性のご説明からサンプル提供まできめ細かく対応します。必要に応じて樹脂メーカーとも連携し、最新の材料情報やデータに基づいたご提案を行います。
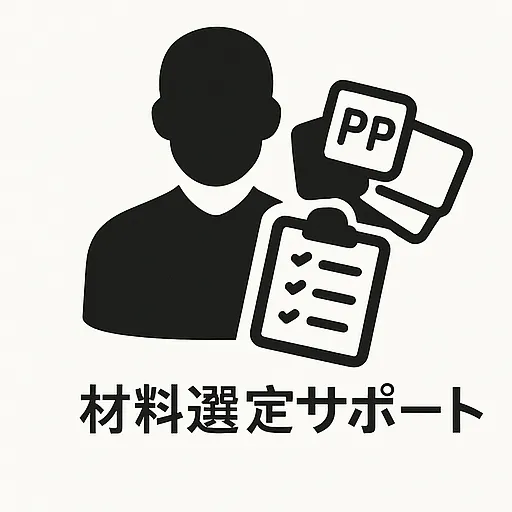
この他にも、量産金型設計の支援や各種CAE解析サービス、アフターサポートまで含め、弊社はワンストップで樹脂化ニーズにお応えします。金属から樹脂への置き換えによる軽量化をお考えの際は、ぜひ当社までご相談ください。